Manufacturing excellence
Thorlux is proud to manufacture over 90% of its luminaires at its Redditch, Worcestershire, UK facility. With complete control over the manufacturing process, Thorlux can minimise negative environmental impacts while conserving energy and natural resources. A multi-million-pound investment has allowed the business to modernise its manufacturing capability whilst increasing efficiency.
The company constantly challenges itself to find new ways to reduce waste through cumulative process improvements. For example, it is working to reduce and eliminate single-use plastics, as well as streamlining and optimising many of its operations throughout the facility. A four-day week has also been adopted in the spray shop, reducing the amount of gas used in the drying ovens through improved efficiency.
Several Thorlux employees have passed the Green Belt Lean Six Sigma training course. Lean Six Sigma is a method that relies on a collaborative team effort to improve performance by systematically removing waste and reducing defects or mistakes. Over a dozen lean manufacturing apprenticeships are currently in progress, and the company is also exploring Yellow and Black Belt Lean Six Sigma training.
Solar energy system
As a part of its carbon reduction initiatives, Thorlux has installed solar photovoltaic (PV) units on the roof of its manufacturing facility.
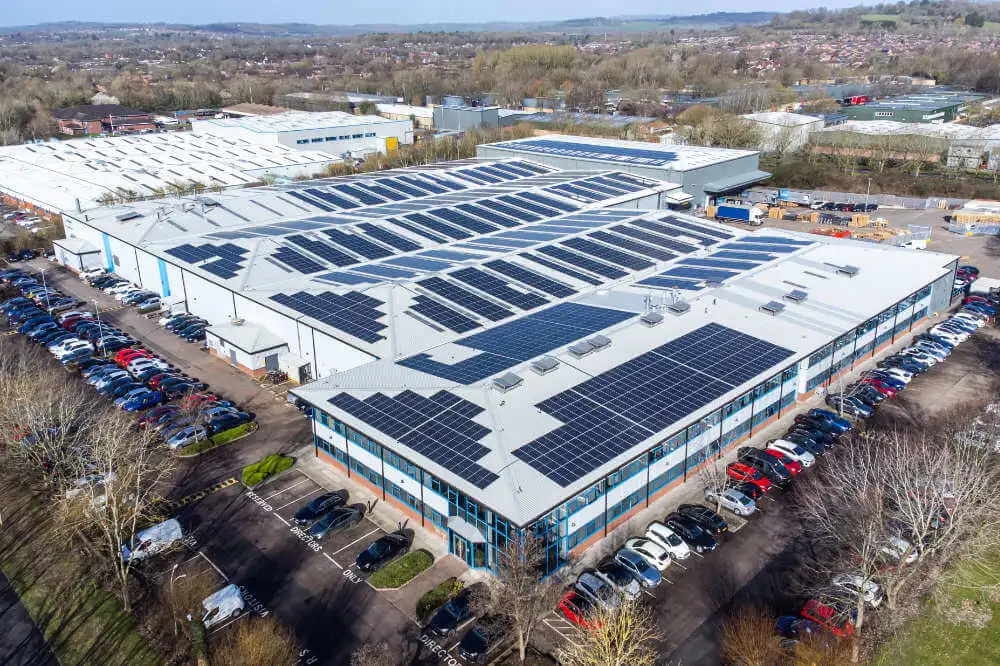
The original Thorlux solar installation came online in 2019 and supplied around 225,000 kWh of electricity yearly. Thorlux considerably expanded the solar grid in 2023; it now delivers an impressive 1 million kWh annually from 3,138 photovoltaic panels.
This electricity helps power the plant and equipment and charge the company’s fleet of hybrid and electric vehicles. On days with lower demand, Thorlux feeds excess energy captured into the national grid. On good weather days, our whole facility can be powered just from the PV system. Over its anticipated 25-year operational lifetime, the solar PV system will avoid the creation of approximately 4856 tonnes of carbon through reduced consumption.
Combining the PV grid with other green electricity supplies means the Thorlux factory and offices run on 100% renewable electric sources.
Live
Solar Photovoltaic Data
Last updated: 28-Dec-2024 10:50:25 (Europe/London)
1 MWh (megawatt-hour) = 1,000 kWh (kilowatt-hour)
Packaging at Thorlux
Thorlux is working to eliminate plastics, increase recycled content and reduce its overall use of packaging.
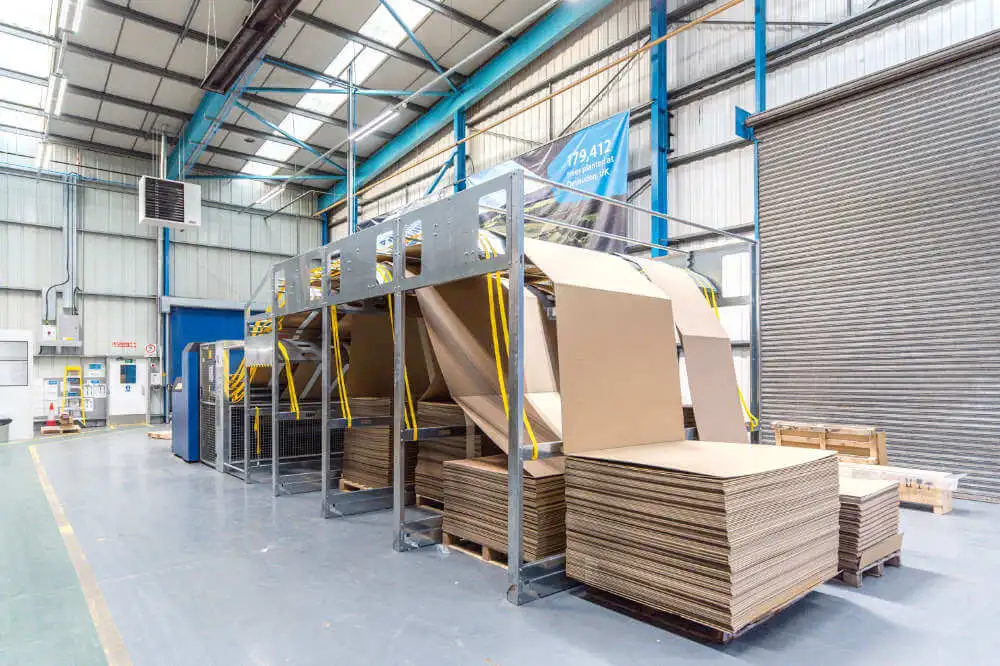
Box-making machine
Thorlux has recently installed a new box-making machine, providing the flexibility to produce specific packaging for luminaires and equipment as required. This eliminates wasteful stockpiling and saves valuable space. Thorlux only uses 100% recycled, biodegradable, Forest Stewardship Council (FSC)-certified cardboard to ensure the highest level of sustainability. Card offcuts are baled and recycled. Furthermore, paper-based packing tape is used instead of vinyl.
Thorlux has been piloting a cardboard recycling scheme for its luminaire packaging. So far, over ten tonnes of cardboard have been returned, which has been reused or recycled through waste management partners.

Installation guides
Thorlux has moved to digital installation guides, saving over 1.3 million sheets of paper yearly – equivalent to 131 trees. Users can access installation information for the luminaire and the lighting control system by scanning a QR code on either the packaging or the product.
Discover our recent recycling initiatives
Thorlux constantly assesses its manufacturing processes to improve resource efficiency and reduce waste. Working with our waste partner, currently 89% of all waste is recycled with zero waste going to landfill.
Thorlux vehicle fleet
Thorlux has a fleet of lorries and vans to deliver its products in the UK. These vehicles use the latest engine technology and are Euro 6 and ultra-low emission zone (ULEZ) compliant.
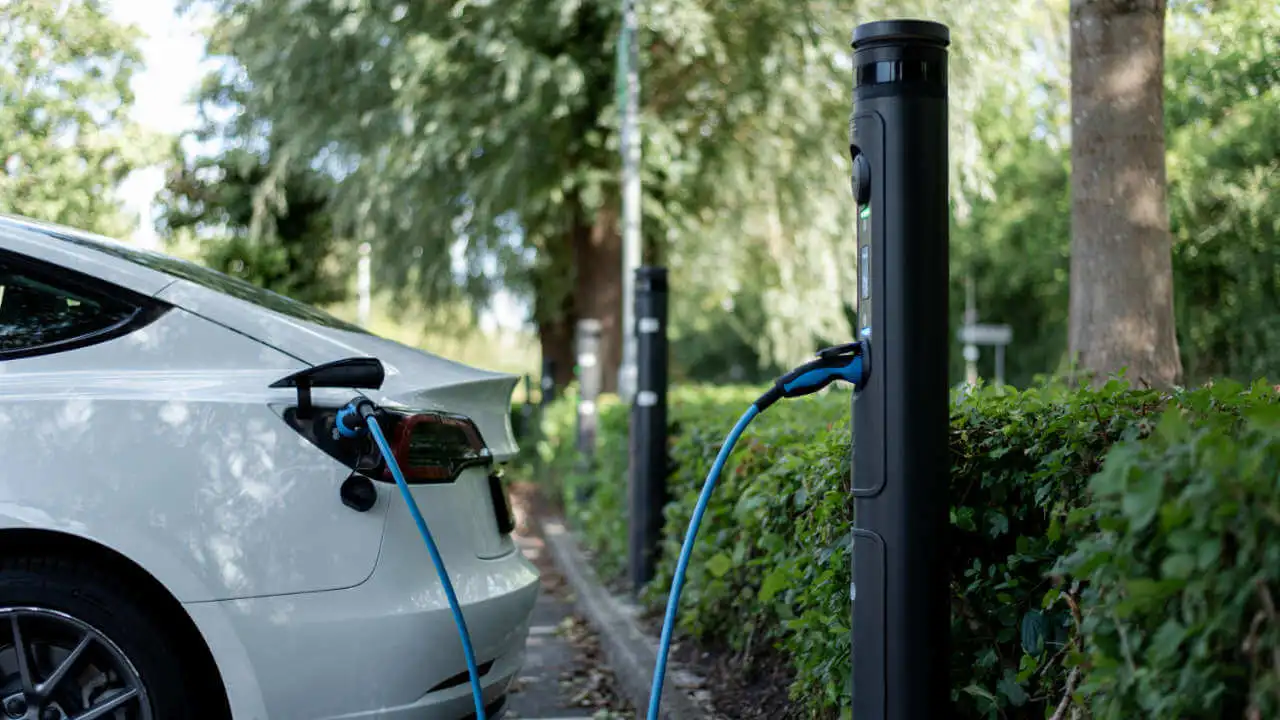
Over 70% of company cars are hybrid or fully electric vehicles (EVs). Thorlux has a proactive policy to increase its use of EVs, with a growing number of charging points on-site at its Redditch headquarters.
Continuous improvement
Thorlux aims to foster a culture of continuous improvement, encouraging all employees to look for ways to enhance its operations. These include proposing creative ideas to boost efficiency, eliminating unproductive or wasteful work, and conducting thorough assessments of existing processes.
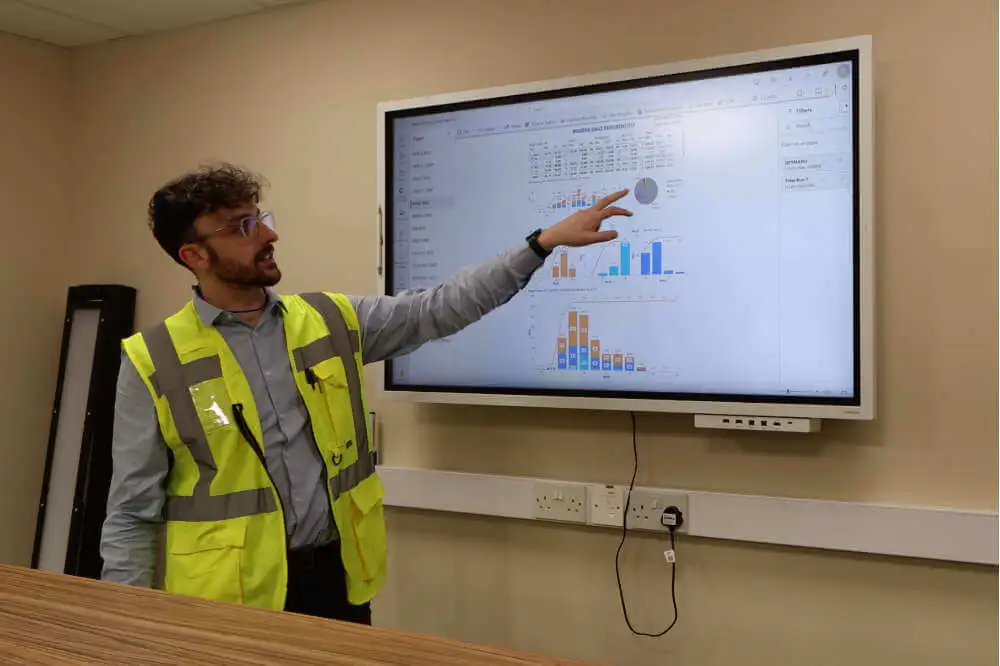
Safety, quality, delivery, cost, and people
Thorlux utilises the SQDCP (Safety, Quality, Delivery, Cost, and People) management tool to enhance operational performance. This framework aids in reviewing, measuring, and improving various aspects of the manufacturing process. Thorlux has implemented a three-tier approach, beginning with individual departments, then a departmental review, and finally, a manufacturing overview, all looking regularly at the SQDCP categories.
These meetings encourage collaboration and ensure the focus is on critical business needs, with a defined chain of escalation if required. Manufacturing teams can identify areas for improvement, implement corrective actions, and ultimately enhance overall operational effectiveness to meet customer demands and improve our sustainability.